Following some feedback from the market, the Cuneo-based company has decided to add lithium batteries to its range of e-WORKERS with lead-acid batteries. The advantages include high energy efficiency, longer service life, fast charging and the possibility of removing the battery in 15 minutes.
At an early stage Merlo decided to use high-performance lead-acid batteries on the e-WORKER. A mature technology, known and used on a large scale in the forklift world, geared towards the operational needs of companies, whether they operate in the industrial, construction or agricultural sectors.
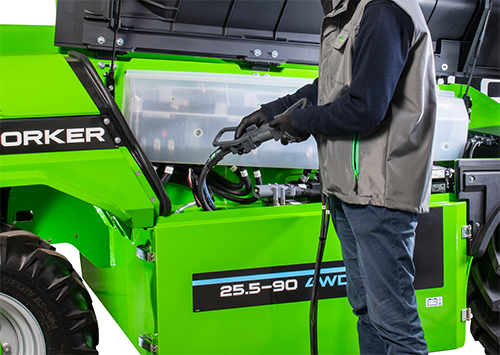
After several feedback from the market, Merlo has now decided to make the e-WORKER also available with a lithium battery pack. This allows Merlo to respond to specific market needs and to be the only company offering the dual lead-lithium configuration.
Lithium batteries have several advantages over lead-acid batteries. They have high energy efficiency, store more energy in a small space, have a longer service life (3000 cycles vs 1800), can be recharged quickly (or partially) reducing downtime and increasing productivity.
Last but not least, lithium batteries require less maintenance than lead-acid batteries and no investment is required in charging rooms or smoke evacuators. The risk of downtime is minimised. The cycle (VDI 2198) used as a standard for measuring the performance of forklifts states an autonomy of 7.5 hours.
The e-WORKER, when equipped with a lithium battery, undergoes some changes. Among these - in addition to a new user interface and stickers on the side - the most important is the BMS activation switch in the cab, next to the armrest, which is used to re-start the battery, equipped with an automatic shut-off system to limit self-discharge. In fact, one of the big differences compared to lead-acid batteries is that lithium batteries are equipped with an actual brain, the Battery Management System or BMS, which performs several functions that control and monitor the behaviour of the lithium battery within the application in real time. Being a much lighter solution than lead-acid, the battery is equipped with a ballast of around 700 kg in order not to unbalance the machine.
Even for machines configured with lithium-ion batteries, the underbody of the machine is free, as the battery rests on only two side supports and is protected underneath by its box. In this way, it can be removed in about 15 minutes using the forks of a forklift, telehandler or pallet truck.
Finally, in order to facilitate the positioning of the forks under the battery, a manual fixture is available whose profile perfectly follows that of the machine's underbody.